Dépassant Tesla, le géant chinois BYD est devenu fin 2023 le plus gros producteur de voitures électriques au monde. Des années durant, il a prospéré sur un modèle néo-fordiste d’intégration verticale, lui assurant un contrôle sur l’ensemble de la chaîne de production – profitant de la dynamique de délocalisation et de sous-traitance qui prévalait en Occident. Les subventions étatiques de l’État chinois ont fait le reste et BYD pose désormais un sérieux défi aux Occidentaux, dans un contexte de transition énergétique où la voiture électrique est amenée à jouer un rôle croissant. Un enjeu que les États européens feraient bien de prendre à bras-le-corps, plutôt que d’accroître leurs dépenses militaires et d’attiser la psychose d’un nouveau conflit mondial. Par Paolo Gerbaudo, traduction Piera-Simon Chaix.
À la fin des années 1970, les voitures japonaises de marques encore méconnues telles que Toyota, Mazda, Datsun et Honda submergeaient les marchés occidentaux. La haute qualité des produits, les performances en matière de consommation d’essence et les prix raisonnables ont – dans le contexte du contrecoup des chocs pétroliers – rendaient ces marques extrêmement populaires. Les parts de marché des fabricants nationaux ont alors diminué, tandis qu’entrepreneurs et syndicats s’insurgeaient face à cette concurrence considérée comme déloyale.
Face au « choc japonais », les pays occidentaux répliquèrent par des mesures protectionnistes. Pour limiter l’impact concurrentiel sur leur industrie automobile, les États-Unis et le Royaume-Uni ont négocié avec le Japon des quotas volontaires à l’importation, tandis que les pays européens adoptaient des mesures du même ordre. Mais ce n’était qu’un premier pas vers une transformation en profondeur de l’industrie occidentale. Dans une tentative désespérée pour regagner leur compétitivité internationale perdue et pour apaiser les revendications grandissantes de leurs travailleurs, des entreprises du secteur automobile commencèrent à imiter leurs rivaux japonais dans le monde entier. La « méthode Toyota », exposée par l’ingénieur industriel en chef de l’entreprise, Taiichi Ohno, devint l’implacable mantra de tout manager industriel digne de ce nom – alors même que les business schools d’Amérique du Nord commençaient à enseigner les méthodes Kaizen et Kanban de la production dite « à flux tendu ».
Cette évolution culturelle, parfois décrite comme un processus plus large de « japonisation », a servi de catalyseur à l’adoption de ce que les sociologues ont fini par appeler les « stratégies de management post-fordistes ». Centrées sur la flexibilité et la réduction des coûts, ces stratégies rejettent les modèles de production à intégration verticale sur lesquels se reposaient les leaders américains et européens du secteur automobile dans les années 1950.
Près de cinquante ans après ce « choc japonais », l’industrie automobile contemporaine est à présent confrontée à un bouleversement bien plus systémique, que nous pourrions appeler le « choc du véhicule électrique chinois ». Jusqu’à encore récemment, l’industrie automobile chinoise, considérée comme une pâle copie des modèles occidentaux et japonais, attirait peu l’attention. Pourtant, elle a fini par atteindre une qualité remarquable dans le secteur stratégique des véhicules électriques, tout en proposant des prix compétitifs. En 2023, les 3 millions de véhicules à nouvelle énergie (catégorie réunissant véhicules électriques à batterie et véhicules hybrides, ndlr) du géant chinois BYD ont permis à ce dernier de coiffer Tesla au poteau sur le nombre de voitures électriques vendues. Et cette même année, les exportations chinoises de véhicules à nouvelle énergie ont augmenté de 64 %. Grâce à de bonnes ventes de véhicules à moteurs à combustion interne et à la hausse de la demande russe induite par les sanctions occidentales, la Chine a déjà dépassé le Japon en tant que plus gros exportateur d’automobiles du monde.
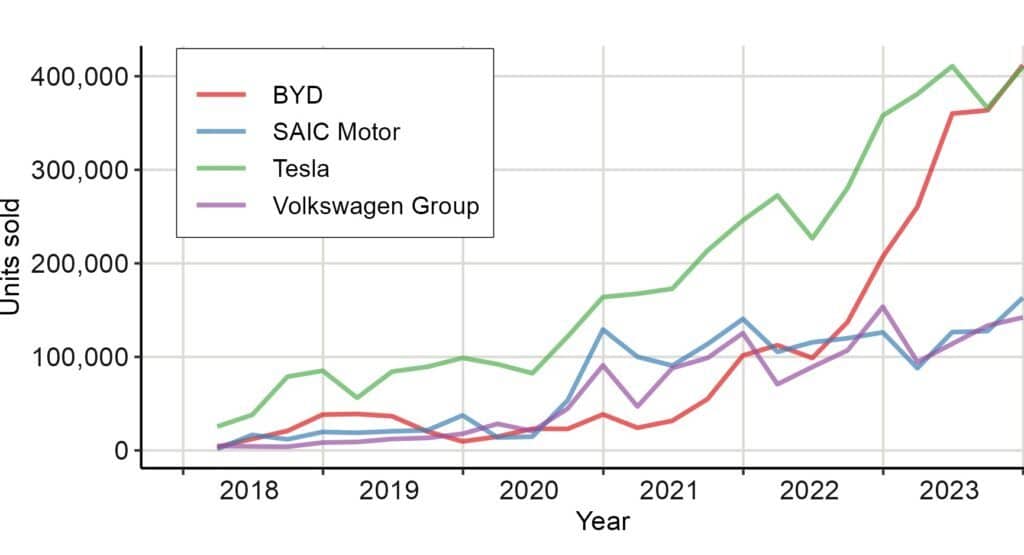
Les stratégies adoptées par les gouvernements occidentaux face à ce nouveau défi concurrentiel, dans un secteur depuis longtemps considéré comme un baromètre des prouesses économiques, sont une question centrale pour le XXIè siècle. Aux États-Unis comme dans l’Union européenne, la percée des véhicules électriques chinois a suscité des accusations de pratiques déloyales. Annonçant en septembre dernier une enquête sur les liens entre aide étatique et succès chinois dans ce secteur, Ursula Von der Leyen a affirmé que celle-ci résultait d’une « manipulation de marché ». Dans le même ordre d’idées, Joe Biden s’est engagé à empêcher les véhicules électriques chinois d’« inonder [le] marché [américain] », tandis que Donald Trump a décrit l’impact des voitures électriques chinoises comme un « bain de sang » économique.
Derrière ces remarques incendiaires se trouve une transformation industrielle non moins significative que celle impulsée par les fabricants japonais d’autrefois. La percée de l’industrie des véhicules électriques chinois a non seulement été permise par de généreuses subventions gouvernementales, mais aussi par de profonds changements de stratégie et d’organisation – en particulier par la résurgence notable de l’intégration verticale, que ce soit au niveau de chaque entreprise ou de l’État.
BYD constitue une manifestation emblématique de cette évolution. L’entreprise a en effet cherché à contrôler tous les aspects de la chaîne de valeur, depuis la technologie des batteries – son cœur de métier originel – jusqu’aux puces électroniques, en passant par les mines de lithium et les rouliers (navires transportant des voitures, ndlr). Enfin, l’entreprise bénéficie d’un coût de la main-d’œuvre significativement plus faible en Chine qu’au Japon, en Allemagne ou aux États-Unis.
Cette approche néo-fordiste a permis à BYD de tirer les coûts vers le bas, tout en coordonnant et en accélérant l’innovation pour plusieurs composants essentiels. De plus, cette approche a permis à l’entreprise d’atténuer les incertitudes opérationnelles et de remédier aux pénuries de différents facteurs et services entrants, comme celle des puces électroniques qui se prolonge depuis 2020.
En parallèle, le gouvernement chinois favorisait l’intégration verticale au niveau national. L’objectif fixé par le plan « Made in China 2025 » – dont l’ambition est de renforcer la suprématie technologique chinoise – est que 80 % de la chaîne de valeur des véhicules électriques soit effectivement située au sein du pays. Bien que le modèle soit susceptible de changer en fonction de l’évolution des relations au sein de l’entreprise, ce tournant vers une « réintégration » et un « re-internalisation » est lourd d’enseignements pour l’avenir de la politique industrielle.
La révolution du véhicule électrique
Selon la célèbre formule du théoricien du management américain Peter Drucker, l’industrie automobile est « l’industrie des industries ». Pendant plus d’un siècle, la fabrication de voitures s’est érigée en baromètre du développement industriel, mesuré à l’aune de la complexité des facteurs entrants, des industries complémentaires nécessaires et des exigences élevées en termes de capital et de connaissances.
La production automobile est non seulement dépendante des secteurs de l’extraction, des produits chimiques, de l’acier et de l’électronique, mais aussi d’une armée de techniciens et d’ouvriers, de machines et d’usines. C’est une industrie qui est confrontée à une barrière économique démesurée et implique des risques entrepreneuriaux majeurs. Tout ceci explique pourquoi relativement peu de pays peuvent prétendre rejoindre le club fermé des fabricants automobiles. Ces obstacles sont encore plus importants lorsqu’il est question de véhicules électriques.
Les véhicules électriques, de même que d’autres technologies « vertes », ne sont pas entièrement nouveaux. Au tournant du vingtième siècle, certaines des premières automobiles étaient propulsées par de rudimentaires batteries plomb-acide ; un tiers des voitures qui circulaient à New York en 1900 étaient électriques. Mais les véhicules à essence ont pris le pas grâce à une meilleure autonomie et à une vitesse plus importante – sans compter son coût de fonctionnement moindre, permis par un pétrole abondant et bon marché. Ces dernières années, cette suprématie du moteur thermique a été sérieusement remise en question.
Outre des performances plus sportives (à l’encontre de la perception du grand public), les véhicules électriques ont des coûts de fonctionnement plus faibles, coûtent moins cher en maintenance et en réparation, sont plus commodes à utiliser et font moins de bruit. Les économies réalisées sur ses coûts de fonctionnement sont éloquentes : les coûts de recharge des véhicules électriques devraient « diminuer les coûts énergétiques d’un véhicule de 50 à 80 % à l’horizon 2030 par rapport à un véhicule à essence comparable ». Bien sûr, en parallèle du déploiement technologique et infrastructurel, des désavantages majeurs perdurent : un coût initial d’achat important, une autonomie moindre, un temps de recharge long et, dans de nombreux pays, des bornes de recharge en nombre limité.
Les batteries électriques constituent – pour reprendre un terme qu’affectionnent les économistes de l’innovation – une « technologie habilitante » des véhicules électriques, mais elles constituent aussi leur goulet d’étranglement potentiel. La batterie lithium-ion, inventée en 1991, a pu se prévaloir de sa taille plus réduite et de sa puissance supérieure pour prendre la place de sa prédécesseure au plomb-cadmium, permettant la naissance de produits jusqu’alors impensables : smartphones, tablettes, aspirateurs, voire des véhicules dits de « micro-mobilité » tels que des vélos et scooters électriques. Le recours à la batterie lithium-ion pour alimenter les véhicules électriques a eu des conséquences proprement révolutionnaires. Depuis son invention, sa densité énergétique a été multipliée par trois, tandis que le coût par kilowatt-heure baissait de plus de 90 %.
La même technologie qui, dans les années 1990, faisait fonctionner les téléphones Nokia et Motorola sert à présent à propulser des voitures, et même des bus. Sans compter que les améliorations permises par la variante lithium-fer-phosphate – sur lesquelles le chinois BYD a une grande avance technologique -, ainsi que le passage d’un électrolyte liquide à un électrolyte solide pour les batteries lithium-ion, pourraient encore améliorer les capacités des batteries.
La place centrale qu’occupent les batteries dans le secteur des véhicules électriques explique pourquoi la construction de gigafactories (immenses usines de fabrication capables de produire des batteries dont le stockage total se chiffre en milliards de watts-heures) est devenue si cruciale, de même que l’accès au lithium. Ce métal alcalin n’est pas rare dans la croûte terrestre, mais son extraction n’est économiquement viable que dans les quelques rares endroits du monde où sa concentration est suffisante. Le Chili, l’Argentine et l’Australie sont à ce titre les nations les mieux pourvues. Afin de sécuriser leur accès à cette matière première, certaines entreprises de véhicules électriques s’immiscent à présent directement dans le secteur de l’extraction du lithium, par l’achat de parts ou en tant qu’actionnaire unique.
Le nouveau Henry Ford
L’émergence de l’industrie automobile chinoise a engendré environ 140 marques différentes de véhicules électriques, mais seule une poignée d’entre elles peuvent jouer sur le terrain de BYD – qui, en 2023, est devenu le plus important fabricant de véhicules électriques au monde devant Tesla. L’entreprise a été fondée à Shenzhen en 1995 par Wang Chuanfu, un orphelin issu de la région rurale pauvre d’Anhui, qui a étudié la chimie et la science des matériaux. Par de nombreux aspects, le fonctionnement de l’entreprise évoque singulièrement une résurgence électrifiée de la logique fordiste de production de masse : un processus de production à forte intensité de main-d’œuvre, une immense armée d’ouvriers et des méthodes tayloristes d’organisation scientifique de la production.
Surtout, BYD accorde une attention toute fordiste à l’intégration verticale. En son temps, Henry Ford avait acquis des mines de fer et de charbon pour produire de l’acier, des plantations de caoutchouc au Brésil pour produire des pneus (avant que l’invention de la vulcanisation n’élimine le besoin en caoutchouc d’origine naturelle), des mines de sable de silice blanc pour fabriquer les pare-brises, les vitres et les rétroviseurs des voitures et même des forêts pour les pièces de la voiture réalisées en bois. Aujourd’hui, BYD entreprend de contrôler la production et l’assemblage des cellules de batterie, la fabrication des groupes motopropulseurs électriques, les semi-conducteurs et les modules électroniques, voire l’extraction du lithium. L’entreprise fabrique également les essieux, les transmissions, les habitacles, les freins et les suspensions des voitures « en interne ». En réplique aux immenses usines Ford de Highland Park et de River Rouge, BYD a construit de gigantesques usines industrielles destinées à la production de batteries et d’autres composants essentiels, et à l’assemblage des voitures. Quatre d’entre elles se trouvent dans la ville d’origine de BYD, Shenzhen, et vingt autres en Chine, tandis que plusieurs nouvelles usines sont en cours de construction à l’étranger, de la Hongrie au Brésil.
BYD entreprend de contrôler la production et l’assemblage des cellules de batterie, la fabrication des groupes motopropulseurs électriques, les semi-conducteurs et les modules électroniques, voire l’extraction du lithium.
Pendant toute la première partie du vingtième siècle, l’intégration verticale a permis à Ford et à d’autres entreprises de réduire leurs coûts d’intermédiation, de contrôler la production et de coordonner l’innovation tout au long des différentes étapes de la fabrication, depuis l’acquisition de caoutchouc et d’acier jusqu’à la standardisation des pièces et des fournisseurs. Une production importante et des salaires élevés dans le contexte d’un marché oligopolistique ont assuré des profits stables dans un environnement macroéconomique en expansion, pendant une période qui, entre la Deuxième Guerre mondiale et la fin des années 1960, a constitué l’ère dorée du fordisme.
La crise pétrolière des années 1970 a mis en évidence la rigidité d’un tel modèle industriel, alors que l’inflation des salaires et la demande en véhicules plus performants ont mis un frein à la compétitivité des fabricants d’automobiles états-uniens. Les industriels occidentaux se sont alors inspirés du modèle d’entreprises japonaises comme Toyota, qui pratiquait une production flexible à flux tendu en s’appuyant sur un réseau de fournisseurs et du personnel externe pour absorber les chocs du marché, externalisant la production de composants. Les fabricants japonais d’automobiles ont divisé la chaîne de montage en îlots de production supervisés par des équipes distinctes. Cette logique organisationnelle a permis de discipliner plus efficacement la force de travail et de désorganiser les syndicats, dont les pouvoirs de négociation se sont effondrés lorsqu’ils se sont avérés incapables de menacer d’arrêter le travail des différentes étapes de la production.
L’externalisation s’est accompagnée de la délocalisation d’une bonne partie de la chaîne de valeur vers des pays où le coût de la main-d’œuvre était moins élevé. L’économiste Raphaël Chiappani a ainsi pu déclarer que « depuis la fin des années 1980, les fabricants d’automobiles en Europe, au Japon et aux États-Unis, tels que General Motors, Ford, Toyota, Honda, Volkswagen, Audi et Daimler Chrysler, ont délocalisé et augmenté la part de leur production automobile vers des pays émergents afin de tirer partie de coûts de production moindres. » Tout cela a entraîné une « division internationale du travail », ou plutôt une « fragmentation internationale », c’est-à-dire que les différents pays se sont spécialisés dans différentes étapes de la chaîne d’approvisionnement, en fonction de leur avantage concurrentiel. Dans la perspective d’améliorer la qualité tout en réduisant les coûts, cette évolution a également eu pour conséquence de rendre les fabricants d’automobiles vulnérables aux perturbations de la chaîne d’approvisionnement. Un risque qui devrait continuer à s’accroître en cette période de tensions géopolitiques mondiales.
Le retour de l’intégration verticale
Les faiblesses de la chaîne d’approvisionnement mondiale sont devenues encore plus apparentes après la pandémie, dans un contexte d’une concurrence sécuritaire accrue. Des termes comme « délocalisation » et « internalisation » ont fait leur apparition dans le débat public. BYD constitue, à cet égard, une manifestation contemporaine fascinante de « re-internalisation » de la production nationale – et des relations que ce mouvement entretient avec les nouvelles politiques industrielles dans leur ensemble. L’entreprise adopte une structure typique de conglomérat intégré verticalement, avec une entreprise centrale (BYD Company) qui contrôle plusieurs filiales : BYD Auto, BYD Electronics, BYD Semiconductors, BYD Transit Solutions et BYD FinDreams (la branche responsable de la production des batteries et de différentes pièces de voiture). Si l’intégration verticale est un modèle partagé avec d’autres concurrents du domaine des véhicules électriques, comme Tesla, BYD a atteint d’un degré d’intégration bien plus élevé que l’entreprise d’Elon Musk, qui acquiert 90 % de ses batteries auprès de sociétés comme Panasonic ou CATL (entreprise chinoise, leader mondial des batteries, ndlr). $
La production de batterie était à l’origine le cœur de l’activité de BYD, ce qui lui assure une compétence cruciale en matière de production de la pièce la plus importante et potentiellement la plus innovante des véhicules électriques.
La production de batterie était à l’origine le cœur de l’activité de BYD, ce qui lui assure une compétence cruciale en matière de production de la pièce la plus importante et potentiellement la plus innovante des véhicules électriques. À travers sa filiale BYD Semiconductors, l’entreprise contrôle aussi la production de puces électroniques, ce qui s’est révélé un atout indéniable à partir de 2020, lorsque la pénurie de puces consécutive à la guerre commerciale entre la Chine et les États-Unis a commencé. La société de Wang Chuanfu produit également ses propres pièces en métal et en plastique, a acquis des parts de Shengxin Lithium Group, le premier groupe chinois d’extraction du lithium, et cherche à acheter des mines au Brésil. BYD s’assure ainsi un contrôle sans précédent de son cycle de production. Selon l’entreprise, seuls les pneus et les fenêtres sont entièrement sous-traités. Un rapport du New York Times a mis en lumière que pour la fabrication de sa berline Seal, BYD a produit les trois quarts des pièces. Cette performance impressionnante est sans commune mesure avec le tiers des pièces que Volkswagen parvient à produire pour une voiture électrique comparable, et assure à BYD un avantage comparatif de 35 % en termes de coûts.
BYD est également de plus en plus active dans les étapes situées « en aval » de l’industrie automobile, c’est-à-dire la vente et les services. L’entreprise vient récemment de faire son entrée dans le secteur naval avec le lancement de BYD Explorer 1, un roulier capable de transporter 5000 voitures. Le navire n’est que le premier d’une flotte vouée à l’expansion pour permettre à BYD d’avoir la mainmise sur la livraison de ses produits. Comme dans le modèle fordiste, la stratégie d’intégration verticale de BYD nécessite beaucoup de main-d’œuvre : en seulement deux ans, le nombre d’employés de l’entreprise a doublé pour atteindre 570.000 travailleurs en 2023 (à peine en-dessous des 670.000 employés de Volkswagen et bien davantage que les 370.000 de Toyota).
Court-circuitant le modèle japonais d’une production largement automatisée impliquant des machines coûteuses, BYD a depuis longtemps fait le choix de s’appuyer sur une main-d’œuvre manuelle comparativement peu coûteuse, amenée à réaliser une myriade de microtâches. Cette faible « intensité capitalistique » s’est jusqu’à présent révélée une très bonne recette pour augmenter les revenus et les profits. Mais tout cela est susceptible de changer avec l’augmentation des coûts du travail dus à de la concurrence entre les entreprises automobiles.
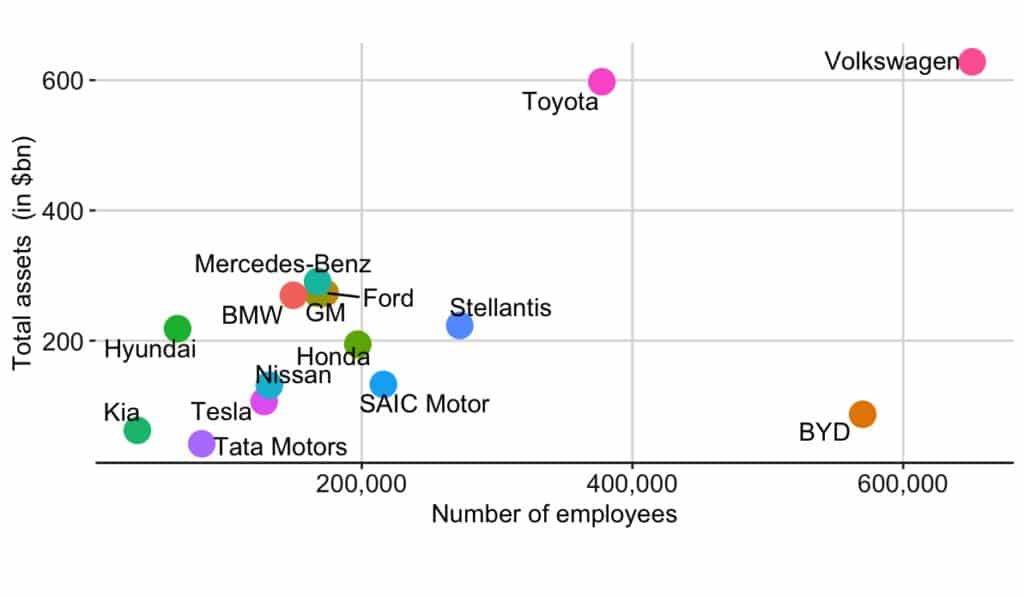
Quelles leçons tirer de la politique industrielle chinoise ?
La réussite de BYD, cependant, s’appuie sur une politique industrielle au long cours. Bien que ses efforts répétés pour atteindre un « développement intensif » dans l’industrie automobile se soient souvent soldés par des déceptions, la Chine a finalement été capable d’exploiter ce que l’économiste Alexander Gerschenkron nomme « l’avantage du retour en arrière ». Tirant des leçons d’autres pays d’Asie du Sud comme le Japon ou la Corée, la Chine a engagé des politiques d’État « développementalistes » afin de passer de la production de biens bas de gamme à des biens haut de gamme, en accordant une importance particulière aux technologies « vertes ».
Les véhicules dit de « nouvelles énergies » (hybrides, électriques et hydrogène, ndlr) ont fait leur apparition dans l’agenda politique avec le dixième plan quinquennal (2001-2005). Cependant, ce n’est qu’à la suite de la crise financière de 2008 qu’ils ont « été désignés comme une industrie émergente stratégique, aux côtés du solaire et de l’éolien. » L’année 2015 a constitué un point de bascule important de la politique industrielle des véhicules électriques avec le lancement du plan « Made in China 2025 », annoncé par Xi Jimping et le premier ministre Li Keqiang. Le plan précise que « la production est le cœur de l’économie nationale, la racine à partir de laquelle le pays s’élance, l’outil de la fortification nationale et le ferment d’un pays plus fort. »
Les véhicules électriques font partie des secteurs clefs considérés comme essentiels pour la réussite à venir du pays, comme les circuits intégrés, l’équipement aérospatial et les nouveaux matériaux. Le plan recommandait en particulier que 80 % de tous les facteurs entrants nécessaires à l’industrie des véhicules électriques proviennent de Chine afin de garantir un niveau élevé d’« indépendance » dans la production des véhicules électriques. Cette incitation à un approvisionnement national a énormément façonné les stratégies de production engagées par les entreprises nationales.
La Chine occupe à présent une place en apparence imprenable dans cette industrie : 60 % des véhicules électriques produits en 2023 étaient fabriqués dans l’Empire du milieu.
La Chine occupe à présent une place en apparence imprenable dans cette industrie : 60 % des véhicules électriques produits en 2023 étaient fabriqués dans l’Empire du milieu. De plus, les entreprises chinoises surclassent leurs concurrents traditionnels en matière de coûts de production. La banque suisse UBS a ainsi estimé que BYD bénéficie d’un avantage de 25 %. Comme tous les pays, la Chine doit importer des matières premières, en particulier du carbonate de lithium depuis le Chili et l’Argentine et du cobalt depuis la République démocratique du Congo, mais elle contrôle par ailleurs des éléments essentiels de l’approvisionnement en matières critiques : plus de la moitié de la production mondiale de lithium, plus de 60 % de la production de cobalt et 70 % des terres rares proviennent de Chine. En outre, l’industrie chinoise produit plus de 70 % des pièces des cellules de batteries et des cellules de batteries.
Les deux tiers de la production mondiale de batteries ont lieu en Chine, CATL et BYD représentant plus de 50 % de la production mondiale. Cette impulsion vers une chaîne de valeur indépendante et largement autosuffisante s’est avérée visionnaire pour permettre d’anticiper les perturbations auxquelles fait face la chaîne de valeur mondiale à cause des événements climatiques extrêmes, des guerres et des rivalités croissantes entre grandes puissances. La part importante de la chaîne de valeur des véhicules électriques qu’elle contrôle offre à la Chine un avantage comparatif significatif vis-à-vis de ses concurrents, tout en lui permettant de défendre une suprématie en matière d’innovation et de propriété intellectuelle qu’elle devrait certainement atteindre dans les années à venir.
Le gouvernement chinois a encouragé ces évolutions en finançant généreusement les domaines des sciences et des technologies, par exemple avec le « Programme 863 ». Sous l’influence de l’ingénieur automobile Wan Gang, ministre de la Science et de la Technologie entre 2007 et 2018, la Chine a largement soutenu le secteur des véhicules électriques. Des joint-ventures, comme celle de SAIC-Volkswagen, ainsi que des acquisitions de fournisseurs de voitures occidentaux, ont permis au gouvernement chinois d’assurer des transferts de technologies détenues par des entreprises étrangères. Le gouvernement a également accordé des bourses ou des prêts à des entreprises automobiles pour, entre autres, créer des usines de production et prévenir les banqueroutes. L’instrument politique incontournable, cependant, est bien le recours à la subvention.
On estime ainsi qu’entre 2009 et 2017, le gouvernement chinois a dépensé 60 milliards de dollars en subventions destinés aux véhicules électriques. Les subventions destinées aux consommateurs, composées en partie de crédits d’impôt nationaux et de crédits d’impôt octroyés par les gouvernements locaux, ont été plus généreuses que les 7.500 dollars de crédits d’impôt mis en place par l’Inflation Reduction Act de Joe Biden. Les 23 gouvernements locaux chinois (19 provinces et 4 zones métropolitaines) gèrent 70 % des dépenses publiques. Leur politique industrielle consiste à soutenir les producteurs locaux en leur octroyant des bourses, des crédits à taux faibles, des fonds de sauvetage et du foncier. En outre, ils visent aussi les entreprises locales lors des passations de marchés, par exemple en passant commande de voitures fabriquées par l’entreprise automobile locale pour achalander la flotte de taxis de la région.
De plus, de nombreuses entreprises du secteur automobile sont des sociétés d’État. Celles qui sont détenues nationalement sont coordonnées par la commission de supervision et d’administration de Biens publics relevant du conseil des Affaires d’État (SASAC) et sont supposées contribuer à la mise en œuvre des objectifs gouvernementaux. Certaines entreprises d’État, telles que SAIC, BAIC et Chery, sont détenues par des gouvernements provinciaux, réputés pour le soutien qu’ils accordent à des industries défaillantes afin de protéger les emplois et les capacités de production.
Le soutien politique accordé aux « champions locaux » par les autorités provinciales et les interventions incitatives du gouvernement central ont la réputation de provoquer une surcapacité structurelle, à l’image de ce qui a eu lieu dans le secteur de l’aciérie au milieu des années 2010, lorsque le gouvernement central a finalement été contraint d’imposer des fermetures et des regroupements. S’il est possible d’envisager la surcapacité comme une perte économique, elle stimule également une lutte darwinienne pour la survie entrepreneuriale et l’innovation technologique, qui irrigue la compétitivité internationale des champions à l’export. C’est ce que nous réserve à présent le secteur des véhicules électriques, touché par de graves fragmentations. La guerre des prix qui ne saurait tarder va s’intensifier à mesure que les subventions diminueront progressivement et que la demande domestique chinoise continuera d’être faible. Cependant, en offrant aux gagnants éventuels la possibilité d’effectuer de plus grandes économies d’échelle, ce moment de vérité est susceptible de rendre les véhicules chinois encore plus compétitifs à l’international.
L’UE s’accroche encore à une vision post-fordiste et à un espoir nostalgique de ranimer la mondialisation et ses longues chaînes d’approvisionnement.
Le choix de BYD et, plus largement, du gouvernement chinois, d’embrasser une politique industrielle orientée par l’État et de recourir à une production verticalement intégrée reflète une tendance notable, bien que récente, au sein de l’économie mondiale. Joe Biden fait lui-même écho à cette tendance en s’engageant à subventionner l’industrie, tandis qu’à l’inverse, l’UE s’accroche encore à une vision post-fordiste et à un espoir nostalgique de ranimer la mondialisation et ses longues chaînes d’approvisionnement. L’enquête actuelle menée par l’UE sur les véhicules électriques chinois aboutira certainement à la recommandation d’augmenter les droits à l’importation, qui s’élèvent actuellement (avec un modéré 9 %) à un tiers des droits pratiqués aux frontières des États-Unis.
En mars 2024, l’UE a commencé à enregistrer les véhicules électriques chinois passés en douane, ce qui signifie que ces droits de douane pourraient être rétroactifs. Les droits à l’importation n’offriront cependant qu’un répit passager si aucune réflexion plus approfondie sur la structure changeante de la production mondiale n’est menée. Les pays occidentaux devraient réaliser que dans de nombreux secteurs, tels que celui des véhicules électriques, ils sont, pour la première fois dans l’histoire moderne, en mode « rattrapage » vis-à-vis de leurs concurrents plus avancés, qu’ils considèrent aussi comme des rivaux géopolitiques clés. Plutôt que de concentrer leur attention sur l’augmentation des dépenses militaires et d’attiser la psychose d’une nouvelle guerre mondiale, les pays occidentaux devraient bien plutôt prendre au sérieux le défi technologique et militaire lancé par la Chine.